Distribution Center Quality Audit with Lyons Quality Audit Tracking System (LQATS)
Distribution Center Quality Audit with Lyons Quality Audit Tracking System
Distribution Center Quality Audit is an assessment conducted to evaluate the operational processes, procedures, and facilities within a distribution center to ensure that they meet specified quality standards and requirements. The primary objective of such audits is to identify areas for improvement, ensure compliance with regulatory standards, and enhance the efficiency and effectiveness of distribution operations.
Distribution Center Quality Audit with Lyons Quality Audit Tracking System
A Distribution Center Quality Audit ensures the efficiency and compliance of operations within a distribution center. Here’s an outline of what a Distribution Center Quality Audit with Lyons Quality Audit Tracking System typically involves:
1. Pre-Audit Planning
- The audit team first defines the audit’s scope, objectives, and criteria. They identify key areas for assessment, such as inventory management and order fulfillment processes, to ensure a thorough evaluation.
2. Documentation Review
- The audit begins by reviewing the documentation related to distribution center operations. This includes standard operating procedures (SOPs) and quality manuals. The audit team checks that the documentation is current, complete, and compliant with relevant standards and regulations.
3. Inventory Management
- The team then evaluates the accuracy and efficiency of inventory management processes. This includes receiving, storing, picking, packing, and shipping operations. The team reviews inventory control procedures, conducts cycle counts, reconciles inventory records, and identifies discrepancies or variances.
4. Order Fulfillment
- Next, the audit assesses the effectiveness of order fulfillment processes. The team checks order accuracy, picking accuracy, packaging quality, and on-time delivery performance. They review order processing procedures, conduct accuracy checks, and evaluate the overall efficiency of order fulfillment operations.
5. Corrective Actions and Improvement Plans
- If the audit identifies discrepancies, non-conformities, or deficiencies, the team initiates corrective actions to address them promptly. The audit findings also help uncover opportunities for process improvements, efficiency gains, and cost savings in distribution center operations.
6. Reporting and Documentation
- The audit team documents the findings in the Lyons Quality Audit Tracking System. The report summarizes observations, corrective actions, and recommendations for improvement. The team shares this report with relevant stakeholders, including management, operations teams, and quality assurance personnel, to foster collaboration in addressing issues and driving continuous improvement in distribution center performance.
Through this structured process, the Distribution Center Quality Audit ensures that operations are efficient, compliant, and continually improving, helping optimize overall performance.
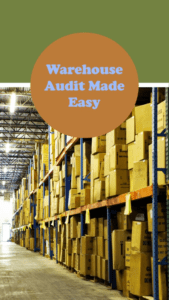
Overall, Distribution Center Quality Audits play a critical role in ensuring the quality, efficiency, and compliance of distribution center operations, as well as in identifying opportunities for improvement and optimization in the distribution process.